Fractographic laboratory
Department of Materials
Faculty of Nuclear Sciences and Physical Engineering
CTU in Prague
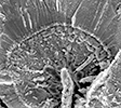
In the fractographic laboratory, the failure processes of diverse materials are monitored, not only metals and alloys, but also ceramics, plastics, rubber or glass (or some biological preparations such as wood or teeth).
From a methodological point of view, as the most important results can be considered the development and verification of a new original method of fractographic reconstruction of fatigue crack development. At present, it is possible to use not only the measurement of the striation spacing, but also the marking of fractures or the unambiguous identification of fractographic features corresponding to selected parts of the load spectrum to reconstruct the time course of fatigue failure.
The content of research and expert tasks solved in the fractographic laboratory is based on the current requirements of scientific research organizations as well as industry. From the application point of view, the most significant results were obtained in solving projects for the aerospace and energy industry.
Aircraft industry
Methods of fractographic reconstruction of the development of fatigue cracks were successfully used in the analysis of fatigue failures, created during the experimental demonstration of fatigue life of fuselages and wings of Czechoslovak aircrafts L39MS, L159 and L410 UVP. At present, verification experiments with a new type of load spectrum for testing the airframe of the newly developed L39NG aircraft are underway in the fractographic laboratory of the Department of Materials.
Energy
At the turn of the century, the fractographic workplace became significantly involved in research activities related to nuclear energy. An extensive experimental program was carried out for Électricité de France and JRC Petten to verify the effect of temperature and environment on the kinetics of crack propagation in materials for nuclear energy. Due to the high quality of the preliminary study, our fractographic laboratory was also selected for further cooperation within the EU. The fractographic laboratory also participates in a number of examinations of service failures of various parts of energy equipment (turbine blades, pipes, steam generators, etc.). The works are commissioned by both power plants (CEZ) and turbine manufacturers (Doosan Skoda Power, Siemens). In particular, analyzes of blade failures of both original turbines of the Temelin nuclear power plant can be considered very important. The results of the analyzes contributed to ensuring the reliable operation of turbines between power plant outages and were also used in the design of new turbines, which have been operating since 2015.